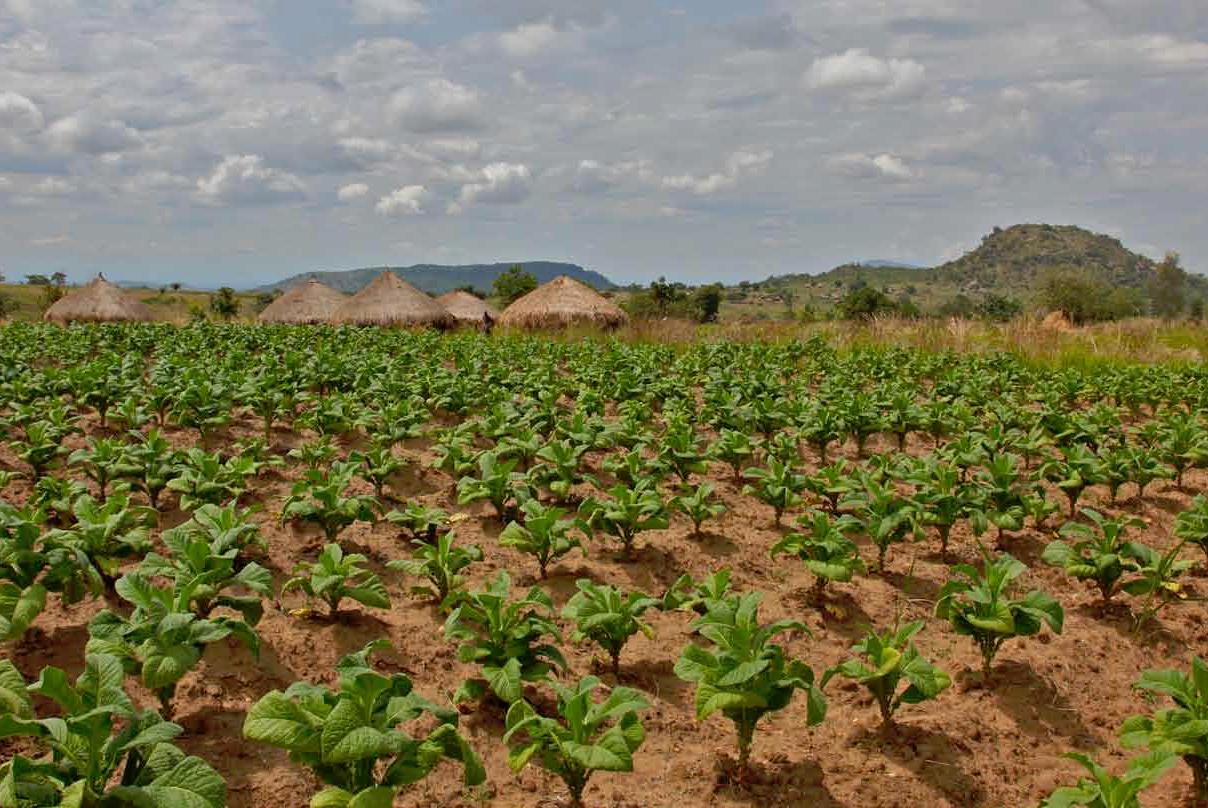
Global tobacco giant British American Tobacco is realigning its supply chain function to improve operational efficiency. Gay Sutton talks to Bernd Meyer, Global Head of Plan, Logistics and Service about bringing these three erstwhile separate functions together.
One of the most challenging tasks facing any organisation is initiating and embedding change. When managers exhibit talent in this field they tend to become corporate trail blazers or trouble shooters, brought in to solve problems or implement changes that will improve the business or develop operational best practice.
When we last spoke to Bernd Meyer of global tobacco giant British American Tobacco he had successfully transformed the massive South African Heidelberg cigarette factory from an underperforming operation based on manual labour to a highly automated and high performing state-of-the-art factory. Along the way, he elevated working procedures, processes and attitudes so that Heidelberg today is an exemplar of British American Tobacco’s culture. At that time, he was preparing to move to corporate headquarters in London where a newly created role awaited him.
“The supply chain at British American Tobaccohas traditionally been split according to the plan, buy, make and move model,” Meyer explained. “We had separate functions for manufacturing, logistics, planning and service and procurement. None of these functions are new. What is new is that we are rolling three of them together as the Plan, Logistics and Service function, leaving just manufacturing and procurement as separate supply chain functions.”
For the past 12 months, as head of Global Plan, Logistics and Service, Meyer has had an enormous and very influential remit. British American Tobaccohas a network of more than 40 cigarette factories in 39 countries, additional contract and license manufacturing agreements and a range of top quality products sold into approximately 180 markets worldwide. In addition to manufacturing, British American Tobacco owns and manages a portfolio of leaf growing operations, thereby managing risk in the supply chain, and actively working to guarantee quality at farm level.
With an organisation of this size and complexity, the company has developed a matrix management structure. The corporate headquarters oversees strategy and companywide functions while decisions are taken as close as possible to the local stakeholders. Each region has implemented the British American Tobacco processes, procedures and best practice, but has the leeway to adapt them slightly to fit with local customs and market expectations.
By folding together the planning, logistics and service departments into a single function the company believes it will achieve significant improvements in efficiency and performance. “Planning is very closely linked with both logistics and service, and the functions were continuously in communication with each other,” Meyer said, “so it made sense to have them operating under the same roof.”
The planning function is very much a strategic one. Operating across British American Tobacco it is responsible for defining the processes and systems by which the company operates, for contingency sourcing and providing a significant input into the global sales and operations planning process. It also conducts global planning for the factories and plans the roll-out of new products and initiatives. The unit therefore examines, standardises and rolls out supply chain processes and procedures across the entire global supply chain. It reviews and defines the optimum global factory footprint, designs the warehouse and supply networks and optimises them to ensure they are always the best fit and will deliver competitive advantage, and it is responsible for global production and logistics planning.
It is therefore easy to see why planning should be brought together with logistics, which oversees the movement and storage of materials at both ends of the supply chain. The logistics function defines logistics strategy, is the primary contact for communicating and negotiating with outsourced logistics partners such as Kuehne & Nagel and DHL, and provides worldwide logistics network modelling, logistics operating standards and best practises for the regions in close partnership with planning.
The same synergies can be found between planning and service, which provides the global marketing function with supply chain support and helps to transform an idea into a commercial product. If, for example, a new product is being proposed the service/innovations delivery department will examine the feasibility of producing it: how and where it will be manufactured, materials sourcing and supply, time frames and lead times, and so on. All of this is done in collaboration with planning where factory footprint, production planning and material sourcing decisions are made.
Meyer’s challenge as head of the new global function is to bring these previously independent sections successfully together and build a fully integrated high performance unit. The process initially began at headquarters in London where Meyer has a staff of 14. “We have designed a blueprint structure for the function, and this is being rolled out in the regions and even to some extent on a local level where planning, logistics and service are now growing together,” he said. “So far, we have establishedgood communication and a close relationship between the global function and the regions, and there is a good sharing of information and experience.” All of which are a tribute to the success of the change management process.
Beyond integrating the three existing functions into a new single corporate unit, Meyer is responsible for continuing to drive business improvement. From the supply chain perspective this entails removing costs from the business, increasing its efficiency and improving environmental performance, all of which are closely interlinked.
Achievements in this area are ongoing and incremental. For example, network modelling is being used to identify where changes can be made to the logistics and warehouse networks to reduce the travelling distances for products. Making changes to product attributes like packaging or format, volumes moved, or even the number of times a product is handled are also helping to reduce costs, and improve efficiency and environmental performance.
Many purely environmental initiatives are also in progress. For example new trucks are specified to incorporate start-stop technology to reduce fuel consumption and emissions, while warehouses are designed to make the most of daylight and to use only energy saving lighting when illumination is required. Considerable work is being done to aggregate purchasing at a regional or even a global level, and this delivers cost savings through bulk purchasing.
“We’re also looking at ways of improving our flexibility and responsiveness to changes in demand, and our speed in rolling out changes quickly. However, improving efficiency is very much about challenging existing ways of working and defining incremental process changes that will improve the efficiency of the whole.” This is a primary function of planning, where new processes are continuously being evolved, designed and then standardised across the entire business.
All core planning, logistics and service functions rely heavily on the company’s world class IT systems. “We useSAP APO, and this gives us complete global transparency with regard to demand and supply figures,” Meyer commented. “Our IT systems obviously also play a very important role in defining and delivering improvement, but human input always has to come first. Before you can execute savings opportunities or alter ways of working, someone has to put a good idea down on paper. And I believe the secret of a successful company in the longer term is how they gather the best ideas from their staff, grow them and replicate them as fast as possible across the business. So improvement is essentially all about communication and people,” he continued.
To achieve this, the company works on the principle that people have to be educated and provided with the right knowledge and expertise, and will then readily identify and propose ways to drive efficiency. Supporting that principle, Meyer’s department works closely with corporate HR designing the content of all training courses for logistics, planning and service personnel, and in some cases his staff also deliver that training. This approach not only raises skill levels, nurtures British American Tobacco corporate culture and cements communication with functional staff from around the globe, but standardises these across the organisation and drives improvements in performance.
As the integration of planning, logistics and service becomes stronger across the organisation, this focus on skills and getting the best from people will become increasingly important. It is a talent that Meyer has honed and demonstrated over many years of successful change management.
Written by Gay Sutton, research by Vincent Kielty
DOWNLOAD
BAT-Europe.Manu-Jan13-Bro-s.pdf